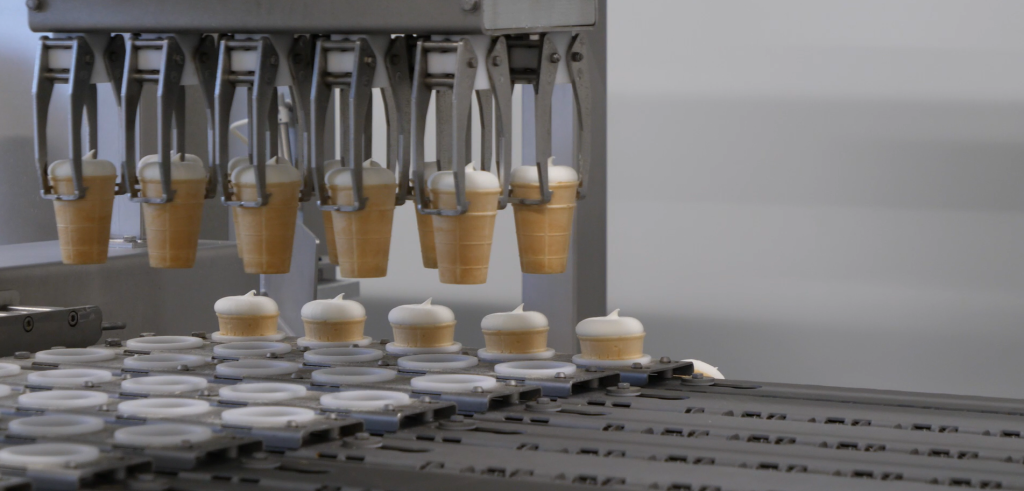
UAB "Art Glacio" is a proactive ice cream producer engaged in the FFR-2 project as a partner company. As usual for food industry, UAB "Art Glacio" uses significant amounts of various detergents and disinfectants to keep equipment clean and ensure hygiene requirements are met.
Although large quantities of hazardous chemicals are used, the company does its best to mitigate chemical risks through managerial means. Moreover, to advance chemical risk management, the company has identified several technical methods to reduce chemical usage and it is already planning the implementation. These identified technical measures will increase resource efficiency when using chemicals to deal with bacteria and viruses in the air of the production facility, on equipment surfaces, and in a separate cold room for ice cream hardening. It is planned that these resource efficiency measures will work in synergy, targeting nearly the same detergents and disinfectants, and leading to a cumulative reduction in use of these chemicals.
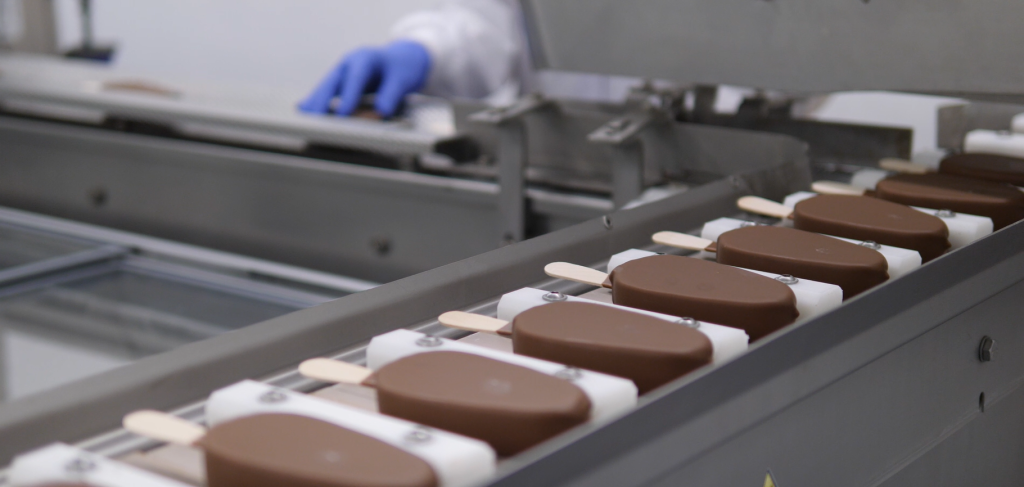
Going into more detail, the first resource efficiency case will employ cold plasma technology to reduce the consumption of air disinfectants and alkaline disinfecting detergents without compromising the required hygiene levels. The second resource efficiency case will enhance the efficiency of cleaning and disinfection processes by adopting a low-pressure foam washing station for the surfaces of production equipment. Lastly, manual cleaning and disinfection in the ice cream hardening room will be automated by installing tubes and spraying nozzles across the ice cream conveyor. Combined, these three resource efficiency cases will not only reduce the consumption of chemicals but also decrease the use of water, personal protective equipment (PPE), reduce worker exposure, wastewater and solid waste generation (e.g., used PPE, plastic canisters, etc.).
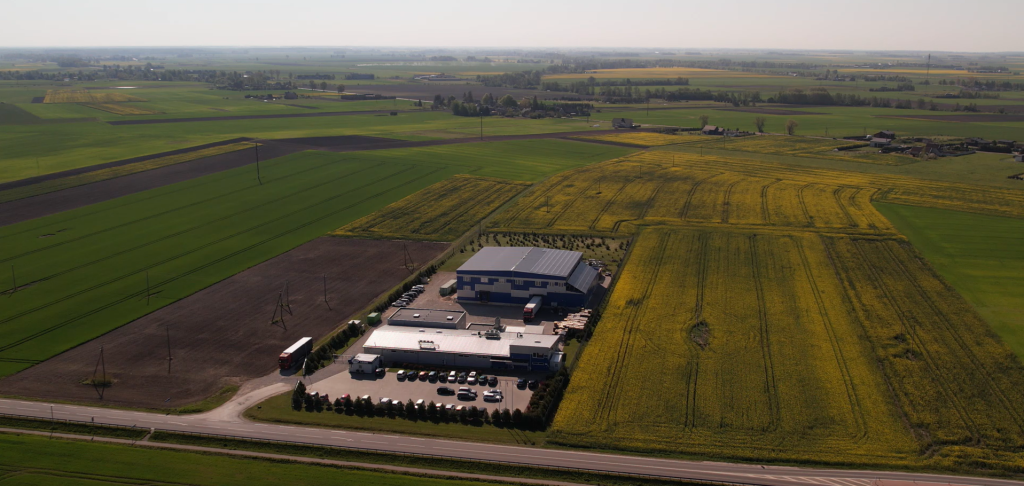
Also, the company will further improve chemical risk management elements by advancing chemicals inventory and raising staff awareness about chemical hazard classes.