AS Paldiski Tsingipada (Zincpot), the partner company of the Life FitforREACH2 project, is one of the largest providers of hot dip galvanizing (or batch galvanizing) service in the Baltics and Scandinavia. After galvanizing, optional surface passivation or powder coatings are offered. The Company aims to offer the best service to metal industry companies. The batch galvanization technology involves several steps, where a number of chemicals are used, including those classified as hazardous.
The goal of participating in the project is to improve the quality of the coating process, thus reducing a share of non-conditional products and increasing related process efficiency, which is expressed in decreased consumption of chemicals and energy, as well as related costs.
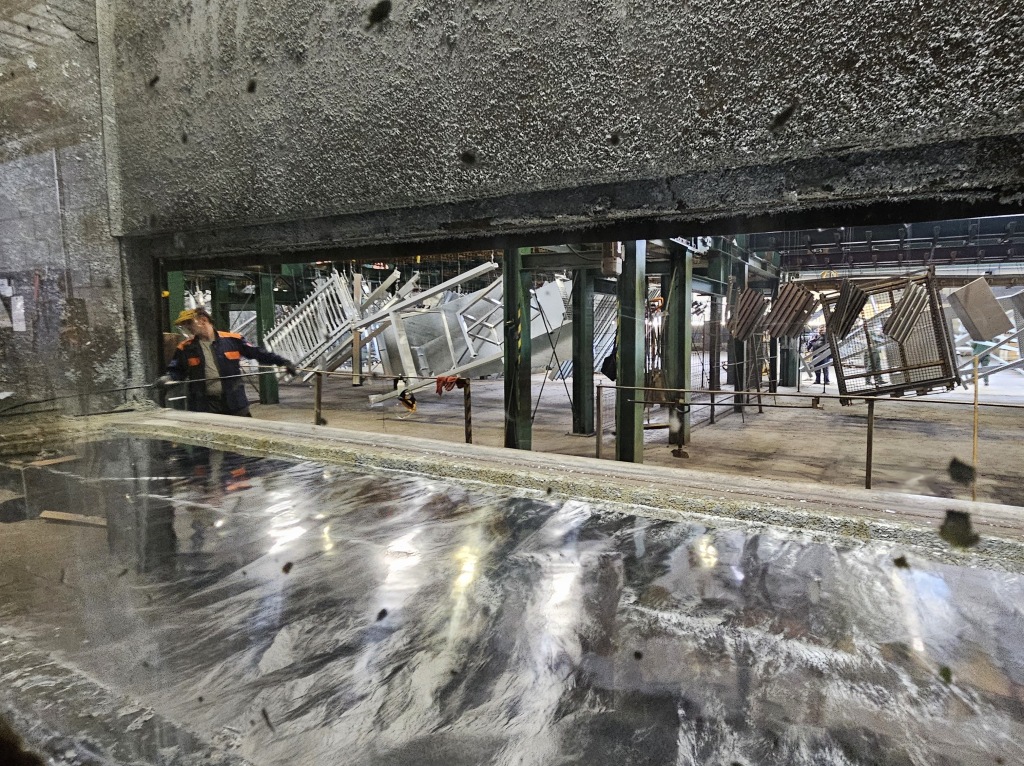
During the project, the composition of the degreasing baths is changed. Manually controlled pumps have been replaced with automatic dispensers, which allows for more precise control of the composition of the degreasing and flux baths. Through the aforementioned steps, the proportion of non-conditional products decreases and less parts require stripping and re-coating. In order to more quickly assess the quality of the surface coating and the impact of production process changes on it, the FitforREACH2 project supports the purchase of a salt-mist chamber test equipment for surface quality monitoring – for testing the durability of the surface coating against corrosion.
The quality, environmental and occupational environment management of AS Paldiski Tsingipada is certified according to ISO 9001, ISO 14001 and ISO 45001 standards. The Company aims to provide environmentally sustainable production. The FFR2 project framework allows to have deeper look into the technical, economic and environmental feasibility of surface passivation and powder coating options using life cycle assessment approach. The results obtained could be later used for composing environmental product declarations (EPDs).
Further, there is a plan to investigate options to use waste stripping as a secondary raw material. Main obstacle to ensure circularity is lack of non-ferrous metal processing companies in Estonia. Transporting of bulk quantities of liquid waste is not economically feasible, in addition it has a large environmental footprint. The Company communicates with potential recycling companies to understand their requirements to accept the waste.